The fastest
way tou your
perfect business
software
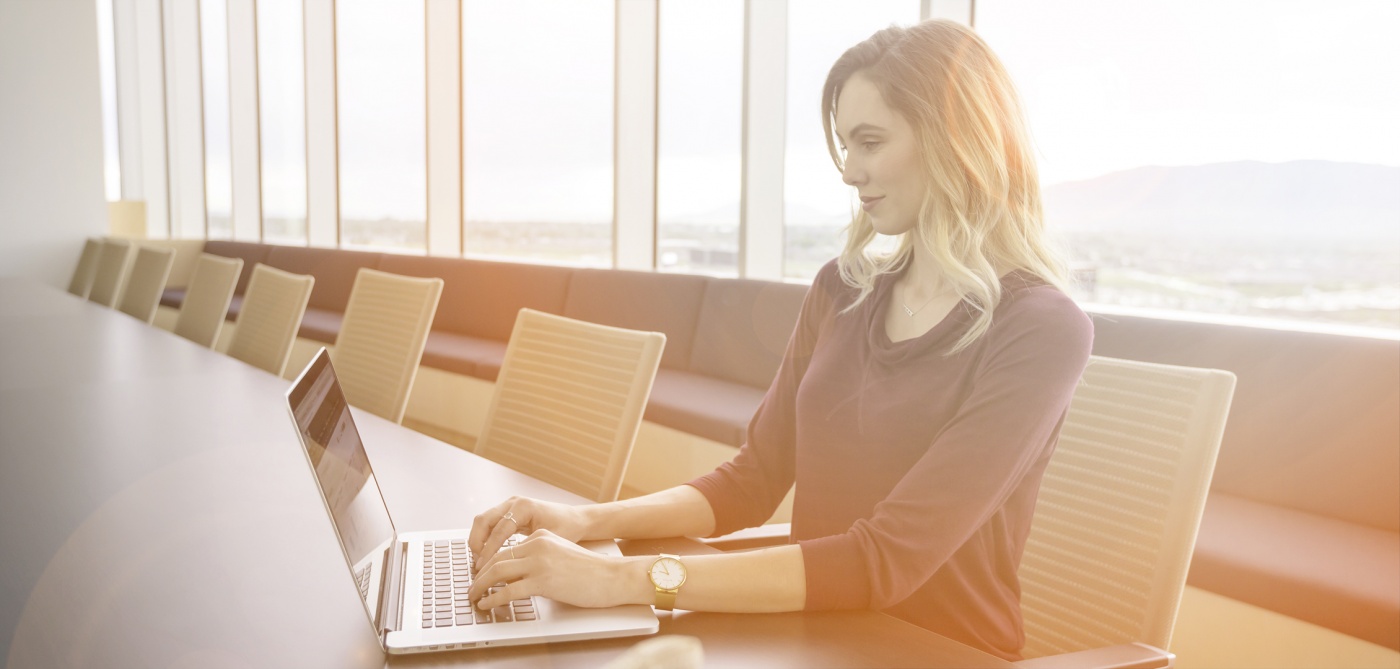
Our tailor-made solutions start at a high level with fully developed standard modules embedded in our business application platform EN4M™. This dramatically reduces time and costs.
Individually developed software tends to be a relatively expensive and risky undertaking. Standard software is often not an option as it is simply not flexible enough to fulfil the company-specific requirements. Our EN4M™ business application platform offers a solution which combines the best of both worlds. We create your customised business software by intelligently adjusting existing EN4M™ modules.
Maintaining a competitive edge with our proven solution of modules from the EN4M™ business application platform.
1. A good foundation with standard modules
Most companies have some internal processes which are unique to them. Nevertheless many processes are similar or even identical from company to company. We do not have to reinvent the wheel. In such cases ready-made standard modules of the EN4M™ business application platform can be used. These modules which have been tried and tested over many years and are still being continually improved are combined on an individual basis according to a modular construction system. This is how we achieve the basis for a high-level solution within a minimum amount of time. s
2. Customising
Once the advantages of standardisation have been fully exploited, we start adapting the software according to your requirements. With our expertise in this process we achieve optimum result
3. We achieve standardised yet flexible solutions in minimal time
EN4M™ individual solutions are quickly realised and impress with their practicality. The flexibility of the system is retained even after completion. Your personal EN4M™ business application can be adapted to new conditions at any time.
A tried and tested system
With the EN4M™ business application platform you are choosing a sophisticated system. Numerous corporations and hidden champions are aware of this already. For over 20 years they have been placing their trust in our expertise as an innovative system provider whenever it comes to tailor-made reference processes and software solutions for complex issues.
Optimum application in minimal time
Analytical and standardised methods dramatically reduce implementation times of new processes and systems in your company. We actively integrate your employees at an early stage. This ensures maximum user acceptance.
A sustainable and scalable solution
Whatever your business development may be, the EN4M™ business application can easily be adapted to future requirements both in terms of complexity as well as performance, particularly with regard to structures, processes, methods and also functionalities.
One central system for a variety of jobs
Business software that offers too little or is not flexible is counterproductive. Gaps are often plugged by drawing on other systems. A tangle of software is the result. This is not the case, however, with the EN4M™ business application platform. It offers multiple functions from a single source and enables fully developed and highly suitable solutions in significantly less time. EN4M™ business applications can easily be integrated into existing system landscapes.
Reference processes
Below is a brief extract of topics based on implementations of optimised processes and our EN4M™ IT solution.
-
Project management
-
Project management
Cross-process scheduling for a bodywork manufacturing process, subject to a Project Master Timing Chart.
- Cross-linked scheduling for selected parts of the process chain (for example project-component-tool set).
- Automatic recognition and communication of deadline conflicts when attempting to change dates, flagged for all linked process partners.
- Automated work-flows for the prevention of process risks initiated for specified events.
- Efficient collaboration via web portal, ensuring straight-forward and secure integration of internal and external partners.
-
Scenario management
-
Scenario management
Prompt assessment of new vehicle development projects using both business management and engineering criteria (for example investment required, anticipated product costs, commonality rating).
- Automatic creation of a range of alternative product designs using stored templates with reference information on technical and business management planning data (for example materials used, manufacturing process employed, required investment, product costs).
- Automatic computation of information relevant to a decision, for example investment, product costs, degree of material utilisation, for a product/product group (for example car bodywork, module, plant, production facilities).
- Automated comparison of alternative scenarios to facilitate recognition of differences.
-
Program and deliverable management
-
Program and deliverable management
Efficient scheduling and management of deliverables in the product development phase, as a preventative measure to safeguard serial production and product quality.
- Across-the-board and cross-process program management by standardised planning and management of gateway scheduling and deliverables, along with their associated dependencies.
- Automatic identification of critical deliverables with regard to planned gateways and SOP to ensure early avoidance of process risks and risks to quality.
- Automatic computation of the criticality of the development project as a whole, with advice on the causes and associated work-flows (drill-down).
- Automated reporting with integrated management information system.
-
Change management
-
Change management
Accelerated scheduling and control of proposed changes concerning the product or production, while also safeguarding the current engineering or production process.
- Automatic recognition and communication of any product changes via interface to BOM and associated automated work-flow.
- Automatic computation of the impact of changes with regard to product costs, investment, deadlines, and quality.
- Online monitoring of all changes of status, investment requirements, changes to product costs, deadline postponements.
-
Production planning and control
-
Production planning and control
Automated and universal manufacturing planning for the bodywork of a vehicle, from the early phase of product development to transfer for serial production.
- Early and continuous targeted information on the engineering and business-management aspects of the manufacturing process, automatically compiled from the manufacturing plans on the basis of prepared knowledge-templates.
- Safeguarding the subsequent serial production by automatic plausibility checks on the technical side to avoid planning errors, with an associated calculation of the maturity level.
- On-going cost and investment control by automatic calculation of investment costs and product costs on the basis of the technical planning data.
- Automatic generation of a work schedule and transfer to production control system for the avoidance of planning errors in the production scheduling.
-
Feasibility management
-
Feasibility management
Cross-process evaluation of the technical feasibility of manufacturing given products, so as to safeguard serial production and product quality at an early stage.
- Automatic calculation of the critical aspects of manufacturing, for speedy identification of risk drivers.
- Process-integrated documentation and assessment of product risks to accelerate and safeguard the assessment process.
- Visualisation of production risks to facilitate smoother traceability of risks.
- Computation of decision-relevant information needed to implement the changes - information such as supplementary investment, increases in product costs, deadline postponements and space requirements.
- Integration of all process partners involved, with an associated automated work-flow and notification system.
-
Material planning and optimization
-
Material planning and optimisation
Optimisation of material usage to reduce product unit costs.
- Structuring, parameterisation and calculation of the differing nesting (positioning of blanks on sheet metal) scenarios for the manufacture of selected shaped blanks, including variants to the scenario.
- Managing variants: Selection of the favoured variants as well as favoured results of a nesting scenario.
- Usage and control of an optimisation algorithm to calculate the cost-optimal nesting layout for a scenario.
- Plausibility check of a nesting scenario, to check if it is filled out sufficiently before doing an optimisation computation. The user is notified of any missing information at this stage.
- Current status checks of nesting scenario, to see whether/which of the used master data (for example blank, materials or plant) has changed since the last computation.
- Integration of a 3D viewer to display the geometry of the blanks and the nesting layout. The nesting layout can be post-adjusted manually by the user and the optimisation newly applied.
- Integration of a quality checker to check the quality of the blank contour.
- Implementation of both scenario and optimisation result comparisons.
-
Product costs management
-
Product costs management
Automatic computation of product costs based on technical and business parameters as well as integrating change management
- Top-down target-planning of product costs to control the target and budget compliance.
- Calculation of product unit costs based on technical and business management planning data.
- Automatic calculation of forecast values for production costs on the basis of identified changes.
- Bottom-up calculation of the actual product costs as compared to the planned and forecast values.
- Automatic calculation of deviation from target values and criticality with associated work-flow.
-
Invest management
-
Investment management
Automatic calculation of investment status on the basis of technical and business management planning data.
- Top-down target-planning of investment to control target and budget compliance.
- Calculation of investment on the basis of technical and business management planning data.
- Automatic calculation of forecast values on the basis of identified changes.
- Bottom-up calculation of the actual investment on the basis of the contracts assigned and/or approved, and amendments in comparison with the planned and forecast values.
- Automatic calculation of deviation from target values and criticality with associated work-flow.
-
Pre-production planning
-
Pre-production planning
Safeguarding of pre-serial startup by transparent planning and management of component requirements.
- Automatic determination of consumer needs.
- Automatic control of the scheduling process with integration of the supplier.
- Automatic control of the finishing process.
-
System integration
-
System integration
Increased efficiency by cross-process system integration.
- Unidirectional integration of production/manufacture bills of materials.
- Bidirectional integration of data updates.
- Bidirectional integration of financial data.
- Unidirectional integration of company master data.
- Bidirectional integration of production planning data.
-
Calculation
-
Calculation
Standardised generation of quotations in a customer specific quote structure incl. template use.
- For the calculation of services, resources can be used together with their costs and possibly different customer end prices.
- For the calculation of products, technical details can be taken into account and be considered in cost and price calculations. This is how, for example, prices for components are determined based on material and production costs and are considered in the calculation.
- Management and use of customer specific price lists.
- Quote specific price corrections or discounts after negotiations
- Margin calculation by quote item
- Definition of templates for recurring service packages
- Standardised customer specific quote text blocks to generate an offer document
-
Issue management
-
Issue management
Efficient planning and control of complex intentions
- Standardisation of intention and action planning
- Intentions are described by the goals and results to be achieved. Acceptance criteria defined for each intention help in measuring goal achievement.
- Simplified and transparent planning of dependencies (“predecessor” or “customer”) between different intentions
- Preventative control of the achievement of process results and identified issues
- Simple control of process results in the context of Gateway planning
-
Demand management
-
Demand management
Standardised control process for IT demands in order to manage demands efficiently and companywide
- Decentralised collection of demands at various locations
- Standardised evaluation and prioritisation of demands
- Evaluation of demands according to costs, investments, appoitments, business case
- Continuous controlling of status of demands by means of stage control
- Document Management Board
- Standardised approval process including several steps, which may be required for example because of various budget limits.
-
Invest & budget planning
-
Invest & budget planning
Standardised, companywide investment and budget planning processes that are integrated in area specific structures incl. Top-down Controlling
- Standardisation of investment and budget planning across all divisions of the company For every single division an individual planning or product structure can be used.
- Technical product structures (such as a manufacturing line with its machines, stations, setups and other equipment) can be integrated for the planning, calculation and control of investment and budget planning.
- Top-down target – commissioning and monitoring, bottom-up cumulation of the detailled investment and budget values.
- Integration of standardised change management as well as budget adjustments
- Integration of purchase orders and order management
- Consideration of project risks and provisions
- Top-down controlling process incl. dashboard and reports
-
Test & validation planning
-
Test & validation planning
Continuous test and validation process, can be evaluated according to preferred aspects, in order to keep an eye on the current quality status.
- Management of test case and requirements library with reference values
- >Generation of requirements with detailed requirement specifications, target values and test results as well as acceptance criteria to ensure the degree of maturity.
- Visualisation of dependencies between requirements and their impact
- Check of dependencies in test plans, direct overview of when which tests are upcoming and when they were carried out with which result
- Allowing for necessary test resources according to availability
- Protocolisation and versioning of test results as well as possibility to save protocols and test specifications as external documents
- Monitoring of planned and actual expense of tests carried out
Example processes, for which EN4M™ business applications have been realized
- Project Management
- Agile Project Management
- Activity Management
- Deliverable Management
- Issue/Topic Management
- Program Management
- BOM
- Production Planning & Controlling
- Feasibility Management
- Material Planning
- Board Planning and Optimization
- Prototype planning
- Boxing / packing
- Budget management
- Tools & dies planning
- Bodyshop planning
- General assembly planning
- Purchase requests & order
- Capacity planning
- Quality planning
- Construction project planning
- Facility management
- Infrastructure management (e.g. streets, sewers, …)
- Risk management
- IT-requirements management
- IT-production planning (KANBAN)
- IT-release management
- IT-ticket support